Semiconductor or chip fabrication plants have stringent requirements when it comes to ultrapure water and the same applies to wastewater treatment. Veolia Water Technologies’ MPPS technology offers efficiency, energy, and water savings when recovering potential resources from waste streams.
As a highly sophisticated technology-led business, the semiconductor fabrication sector sets stringent standards when it comes to its processes. The industry is a heavy water consumer and increasingly, these same exacting standards are also being applied to wastewater treatment. Effluent discharges from chipmaking facilities are difficult to manage, often being heavily contaminated with organic solvents and cutting residue, metals, silicon, acids, and salts.
Silicon wafer fabrication waste streams can contain crystalline silicon sludge, fragments, and cutting oil as well as hydrofluoric acid and materials like copper sulfate solution. A key organic solvent in the silicon fabrication and semiconductor chip production sector is isopropyl alcohol (IPA), which is used in multiple production steps to wash intermediate products.
With the right water treatment processes in place though, many of these contaminants can be recovered, potentially saving significant sums in water treatment and sludge disposal. Furthermore, it also offers potential secondary revenue streams from recovering valuable materials. Selecting an appropriate water treatment technology offers an opportunity to recover silicon, fluoride, copper, and highly concentrated IPA, for example.
Waste streams containing IPA may be treated using distillation columns or ultra-filtration/reverse osmosis (UF-RO). However, both of these solutions have disadvantages. Distillation columns are extremely energy intensive and may also present several operational issues when the column needs to be cleaned, for example.
Meanwhile, UF/RO produces large volumes of reject water (up to 10-25%), which then must be treated, and also demands membranes be regularly replaced.
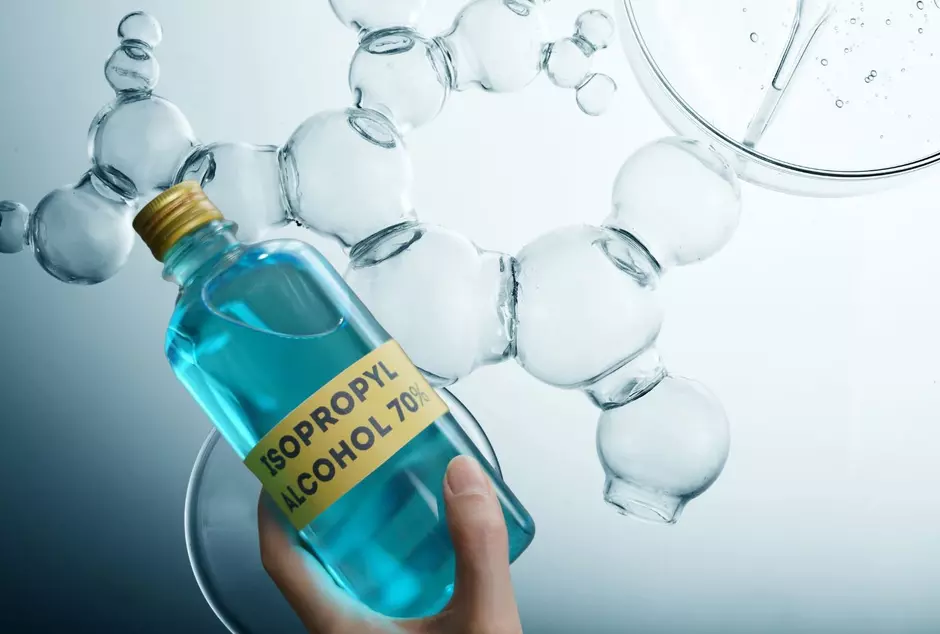
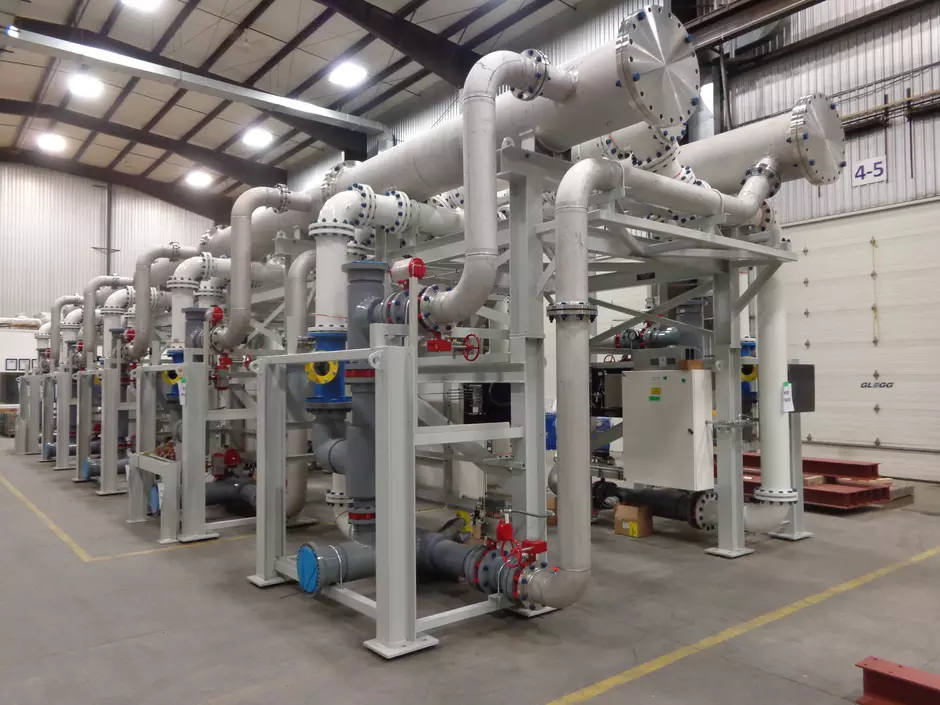
There is an alternative, Veolia’s Macro Porous Polymer Sorption (MPPS) which is a highly effective, proven, and reliable technology for removing dissolved and dispersed solvents from wastewater.
Energy consumption savings
Macro Porous Polymer Extraction (MPPE) is a Liquid/Liquid extraction system in which the extraction liquid is immobilised within the polymeric porous particles. These particles can contain up to 70% by volume of the extraction liquid and are applied inside a packed column. When feed water is flushed through these columns, the solvents migrate from the water into the extraction liquid. However, IPA is a very polar component and has a low affinity for the extraction liquid. Therefore a new type of media has been applied that is based on sorption rather than extraction and is therefore indicated as MPPS. The actual process in which two types of media are being used remains exactly the same and has been used for decades in other industries, in particular, oil & gas.
As the polymer particles become saturated with hydrocarbons that are removed from the wastewater, the column is periodically regenerated by heating it with low-pressure steam. At around 112°C, the hydrocarbons are released from the polymer through evaporation and are subsequently condensed and removed as a liquid phase. Almost all of the hydrocarbons are removed.
The MPPS system uses two columns to facilitate simultaneous extraction and regeneration resulting in a continuous water treatment process and therefore no potential impact on plant production and operations.
Using MPPS to treat wastewater streams containing IPA offers numerous advantages in terms of both capital and operational expenditure. Certainly, energy intensity is much reduced when compared with alternative solutions like distillation. Energy consumption of the MPPS system is only about 10-15% of the equivalent distillation column approach.
Perhaps more importantly though, the efficiency of the process is very high and almost all the IPA can be removed from the waste stream. MPPS technology can reach any required removal efficiency by simply adding more media to the column. Indeed, the process results in a highly concentrated waste stream in which all IPA in the waste stream can be recovered as a 30% solution.
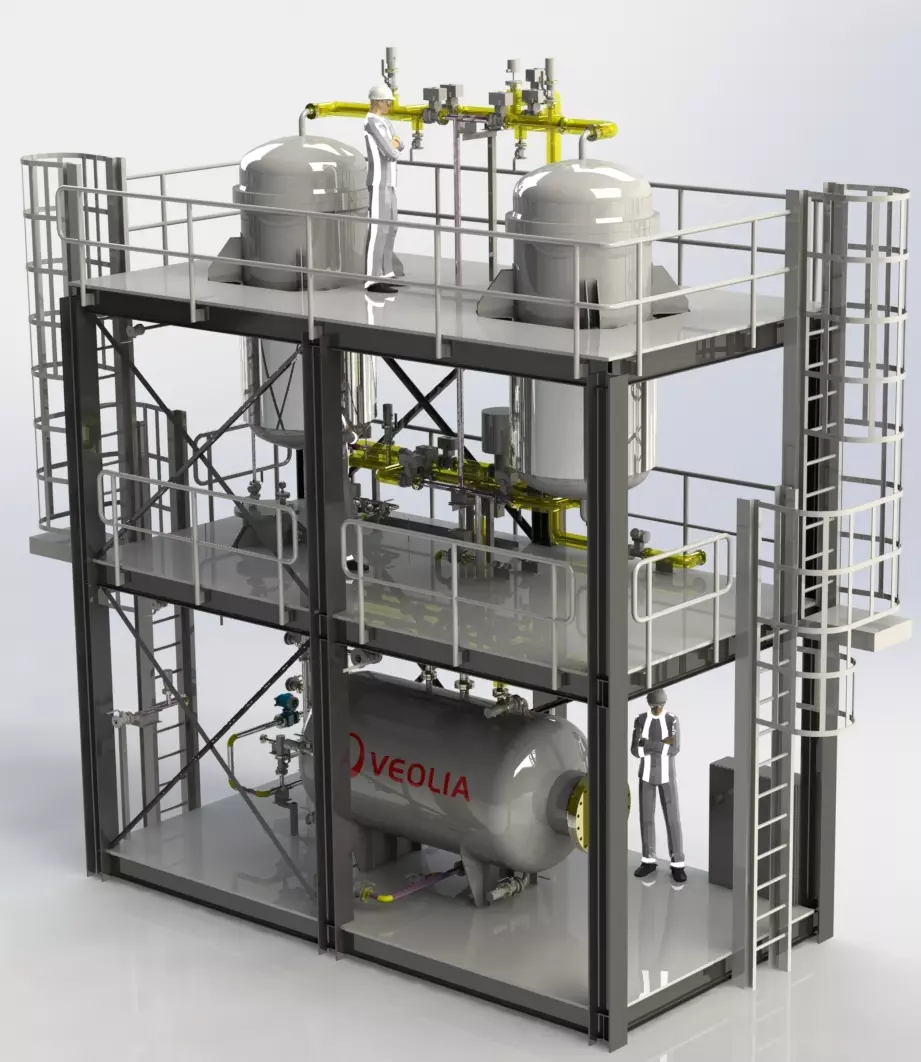
Generating resources from waste
The separation of practically pure solvents/concentrated IPA for reuse means that it typically retains some residual value. There’s a robust market for the production of second-grade IPAturpentine, paint thinners, and as fuel. Furthermore, the IPA may be further purified by third-party operators and reused in the primary processes.
The water recovery rate using MPPS is also better than competing technologies with a recovery rate of up to 99.9%.
The water recovery rate using MPPS is also better than competing technologies with a recovery rate of up to 99.9%. The non-toxic (zero harmful) treated water can then either be further treated, reused for example in condensers, or the replacement of utility water. The MPPS process, therefore, minimises primary water use.
These qualities support the circular economy and help meet corporate social responsibility and environmental, social, and governance commitments. These are increasingly important factors in today’s competitive market, but also represent value for money by reducing water treatment costs and increasing resource recovery.
Overcoming energy and site challenges
In one recently awarded installation in East Asia, four modules will treat wastewater that contains a significant amount of IPA. One of the challenges of the site was the limited availability of power and energy. To avoid major upgrades and investment in the energy system, a technology with a lower energy consumption was required, such as MPPS.
With a concentration of more than 1000 ppm in the waste stream the treated water comes out with IPA in the range of less than 10 ppm, a factor of 100 reduction, or more than 99% removal efficiency.
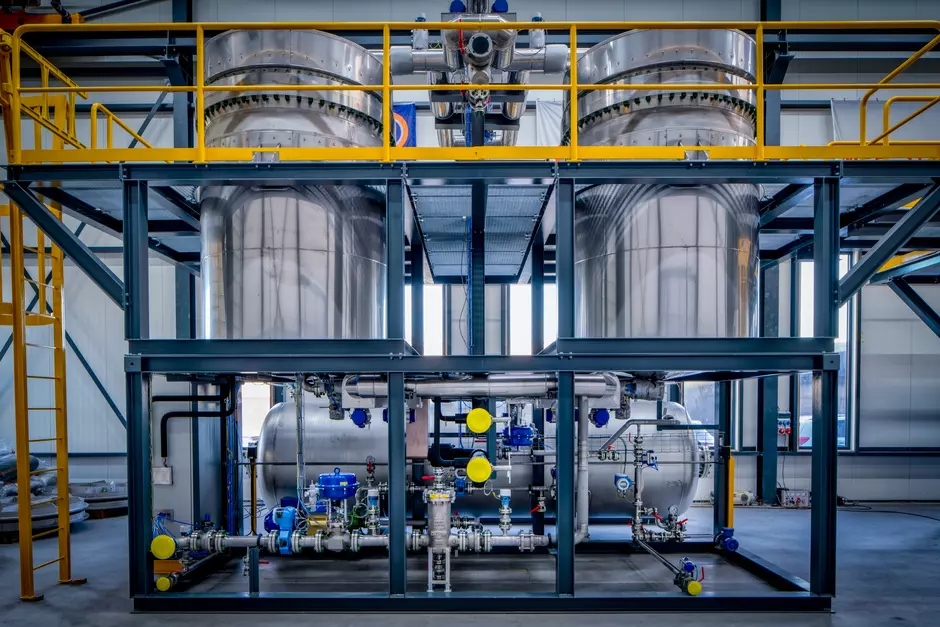
For this particular project, the site also presented major challenges. The designated location was in the basement with limited height and also with limited access. All the MPPS modules had to pass through a shaft 3 x 3.2m square before being carefully turned and assembled together. A distillation solution would probably not fit into such a basement site. Furthermore, the MPPS system is clearly more compact than RO because this approach also needs the UF unit as a pretreatment step.
In many jurisdictions, IPA discharge requirements are extremely stringent and these limits are steadily becoming stricter over time. This is of growing importance as removing these components is simply a regulatory requirement if they are to operate. Moreover, even in these high-value industries, the circular economy is very important for good cooperate citizenship.
MPPS is helping the silicon microchip industry to improve its environmental performance by enabling waste stream components like solvents to be efficiently recovered and recycled, reducing effluent discharges and curbing emissions of greenhouse gases.
As the semiconductor industry looks to adopt alternatives across its whole value chain, MPPS is an innovative solution to help unlock valuable resources, while reducing energy consumption.
Author: Atlantean Media