Missed part I of this article? Check it out here.
With energy and water savings, process efficiency, and considerable operational advantages, MPPE is a technology that offers an efficient solution to some of the most testing industrial waste streams. Now it’s giving new life to pharmaceuticals.
The pharmaceutical industry faces particular and unique challenges when it comes to wastewater. Toxic waste components, like the hydrocarbon solvents used in production and synthesis processes, can make pharmaceutical effluent discharges difficult and costly to manage.
Key drivers to deploy MPPE
Removal of the more complex components from waste streams is a critical driver in deploying MPPE technology. Toxic materials, for instance, cannot be handled by the biotreater in conventional wastewater treatment plants. Efficiently removing those toxic components allows the bulk of the wastewater stream to be passed through a standard biological treatment process or reused on site.
Furthermore, eliminating and concentrating the toxic materials by a factor of up to 200 significantly reduces the volume of waste that may otherwise need to be removed from the production site by a tanker truck for subsequent disposal.
The MPPE solution also consumes much less energy than a distillation process. In fact, only around 10-20% of the energy is needed during a full steam regeneration cycle of MPPE when compared with distillation treatment, even with associated energy recovery.
These characteristics represent clear cost and environmental advantages over other solutions, but there are a number of additional benefits too. Although typically it is used to remove all traces of hydrocarbon solvents, its recovery efficiency means MPPE can be used to extract specific high-value products from a wastewater stream.
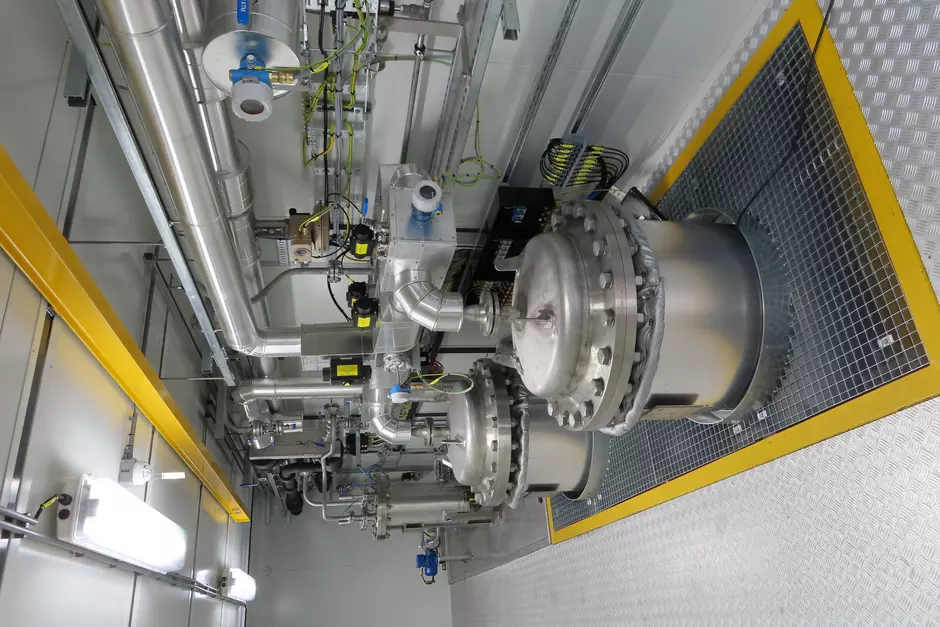
Where hydrocarbon solvent removal is the goal, further treatment and distillation - often by a third party - allows the recovered solvent to be reused in the pharmaceutical process. Indeed, in some cases, the recovered solvent can be reused directly from the MPPE separator.
There are also significant operational gains. Distillation columns can suffer from fouling, and when this occurs, the column must be cleaned using solvents. Under these circumstances, the unit must be taken out of service, which is both a fairly expensive exercise and also presents a number of health and safety challenges. The continuous operation of MPPE avoids these issues.
In one case study, a Scandinavian pharmaceutical plant had been using a conventional distillation column in its wastewater treatment set-up. However, the operation had been dogged by operational difficulties due to fouling in the distillation towers. Energy consumption was also too high, and the company was looking for better alternatives. As a result of the substantial energy efficiency gains and clear operational reliability advantages, when the existing plant was extended, the owner considered MPPE technology. Through laboratory testing, which they witnessed, Veolia was able to prove that MPPE was a much better solution and it was subsequently adopted. In this case, the wastewater treatment plant uses a containerised version of MPPE located close to their tank farm. As a result, this approach doesn’t take up space in the process building.
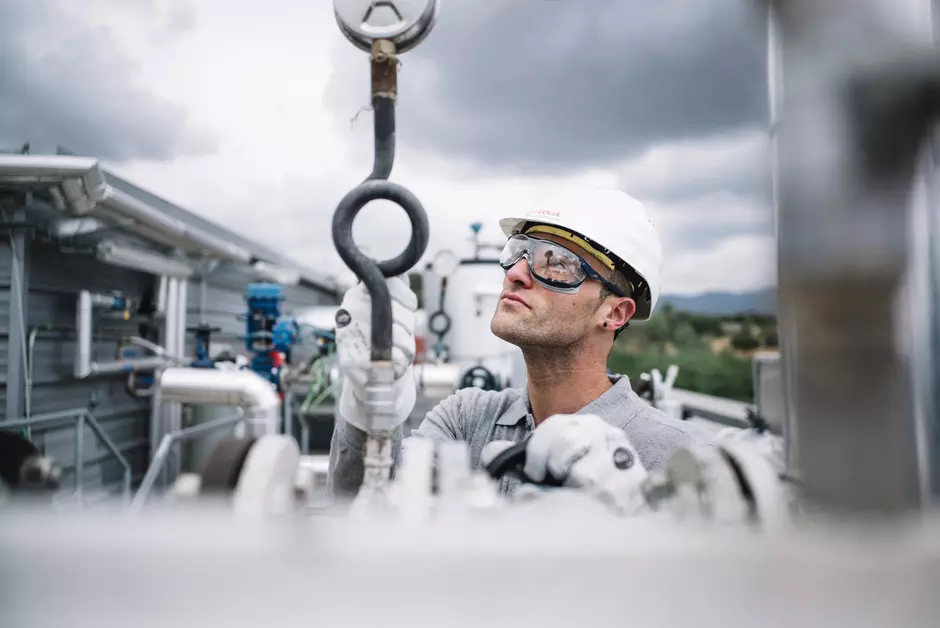
Easing the pain of hydrocarbon recovery
While MPPE is just one range of solutions in Veolia Water Technologies’ portfolio of wastewater systems, it offers numerous advantages when treating the challenging hydrocarbon waste elements arising from the pharmaceutical industry.
Not only is the energy intensity much reduced when compared to alternatives, but the efficiency is very high with almost 100% of the hydrocarbons recovered from wastewater. Water treated with MPPE can then be further purified by other operations, where one of the requirements for those treatments is typical that the hydrocarbon content is very low.
This helps pharmaceutical companies deliver important water savings in their processes but also supports resource recovery of materials like solvents and even specific high-value products within the waste stream. By effectively tackling just one element of the wastewater stream, MPPE can solve a major slice of the wastewater problems faced by pharma and deliver a whole host of benefits.
Ultimately, though, the MPPE process allows pharmaceutical companies to guarantee their business continuity by ensuring that processes and projects are within environmental regulatory limits both now and in the future.
For more information on MPPE, please click here
Author: Atlantean Media